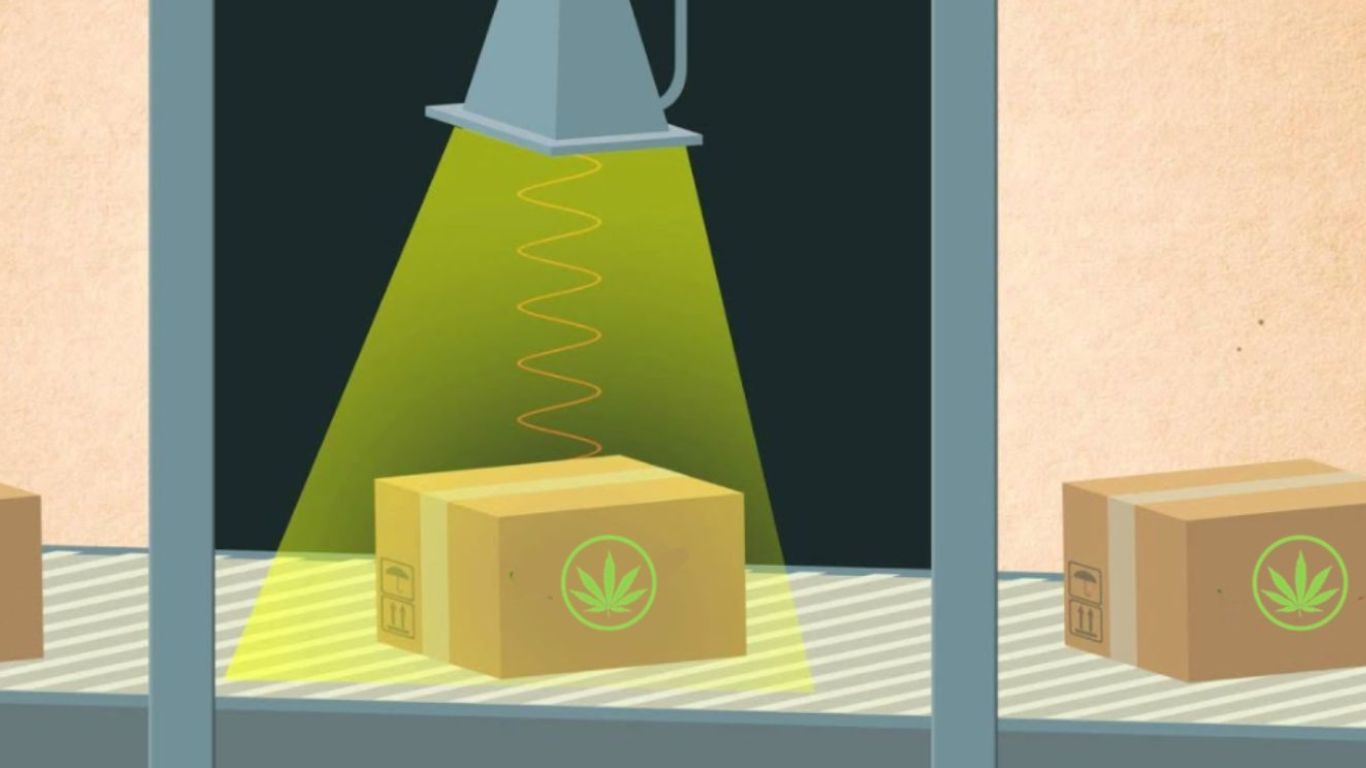
One of the often misunderstood aspects of legal cannabis production is the quality assurance measures many licensed producers take post-harvest to ensure that their product passes a variety of tests. And in the four years since legalization, few have garnered as much attention as the process of irradiation.
Take this Forbes article from April 2022, for example. “Would you smoke ‘nuclear weed’?” asks the headline before quickly (and ominously) answering: “You might already.”
The nuclear weed in question is not, of course, the glowing, radioactive bud image the headline conjures, but cannabis that has undergone irradiation—a quality assurance process, common in both the Canadian and American cannabis industries, that exposes cannabis to radiation in order to bring its microbial levels below regulated thresholds.
“The intent of the irradiation process is not to make up for, or compensate for, really poor sanitation systems or really contaminated product.”
Gordon Dobrindt, Senior Manager Quality Systems, Steris
Irradiation is generally accepted within the cannabis industry as a useful quality assurance process at the end of the production cycle that brings microbial levels under safe thresholds. Many producers routinely irradiate all batches of cannabis as a kind of quality guarantee—not necessarily to bring an unsalable batch up to par, but to provide an assurance that the batch will pass quality tests. “The intent of the irradiation process is not to make up for, or compensate for, really poor sanitation systems or really contaminated product,” said Gordon Dobrindt, senior manager of quality systems at Steris, during an irradiation panel discussion earlier this year. “It’s a final level of insurance.”
But this is far from a unanimous opinion, and critics of how the industry uses irradiation say the process is being “abused” by some producers. Craft producers, meanwhile, are finding that marketing their cannabis as non-irradiated is attractive to quality-conscious consumers coming over from the illicit market.
The public’s understanding of irradiation is spotty. Questions and myths persist about the safety, value, and necessity of irradiation in cannabis production, as well as the impact on the cannabis itself, with many laypersons blaming irradiation for all manner of deficiencies, from dryness, to colour, to poor taste.
When it comes to this oft-misunderstood process, who’s right here? In a way, everyone is.
What is irradiation?
In the simplest sense, irradiation works by exposing harvested cannabis to radiation—commonly either gamma, electron-beam (e-beam), or x-ray—to render contaminants like mould spores and other microbes inert and harmless to the consumer. At the outset of legalization, gamma irradiation was the most common method of decontamination, but since then, some producers have moved to e-beam irradiation, a shorter and cheaper process than gamma that produces comparable results.
There’s little disagreement, even among critics, that the process, which was first used on food in the 1950s, can effectively reduce microbial contamination to safe levels. Irradiation is broadly effective at bringing microbial levels below acceptable, safe-to-consume thresholds. The goal is rarely to sterilize the product completely but rather to bring the microbial levels down. “The limits themselves are pretty strict,” says Siva Kalyan Sompalli, quality assurance technical lead with Aleafia Health. Stripping cannabis of all microbes is unrealistic, he says. “It’s not free of microbes, it’s just that the microbes are within acceptable limits.”
Does it damage the cannabis?
Although a few studies over the years have examined the effect of irradiation on cannabinoids and terpenes, “there really is very limited science out there on this issue at the moment,” says Tess Eidem, a microbiologist and owner of Rogue Micro, a microbial control consultancy in Colorado. “Overall, data is pretty lacking in our industry.”
A 2020 study led by researcher Olga Kovalchuk found that irradiation converted some of the THCa in their samples to THC, as well as noted “changes in several terpenes.” A further study, published in November 2022, found, however, that irradiation “has minimal effects on THCa, delta9-THC and terpene concentrations”—but noted that they achieved that “under well-controlled laboratory conditions” that “do not reflect how cannabis manufacturers may conduct their decontamination procedures.”
Terpenes are a slightly different story. A 2016 study by Bedrocan’s Arno Hazekamp found that “irradiation had a measurable effect on the content of multiple cannabis terpenes, mainly on the more volatile monoterpenes.” The damage was normally found to be in the 10-20% range. “The slight terpene reduction observed in the current study is comparable to the effect that short-term storage in a paper bag had on cannabis samples,” the study found. “A likely explanation, therefore, seems that gamma irradiation slightly accelerates the evaporation of some of the more volatile terpenes.”
But it’s important to note that the degradation of terpenes is not due specifically to the irradiation. “Irradiation itself generates a very small amount of heat,” says Sompalli. “It’s not the irradiation itself that affects the terpenes, it’s the temperature change.”
“You’re growing something that is plant material, in grow mediums where you apply nutrients. You need to have microbes to support plant growth, and that’s the primary source of any microbial contamination itself. It’s a natural balance, a symbiotic relationship.”
Siva Kalyan Sompalli, quality assurance technical lead, Aleafia Health
How are LPs using it?
It’s been estimated that between 80 and 90 percent of Canadian LPs are routinely irradiating their cannabis as a standard practice in order to avoid costly recalls and failed tests. “We are irradiating because we want to guarantee the quality,” said Nina Ackah of Viridis Cannabis during the previously mentioned panel discussion. Microbial regulations are strict. “I believe almost every LP would not be able to meet those limits,” she said. “Irradiation comes in to meet the product specification that we require.”
Producers often claim that their microbial levels can vary a lot, regardless of sanitary practices. Cannabis is a living plant, after all, and microbes are crucial to the process. “You’re growing something that is plant material, in grow mediums where you apply nutrients,” Sompalli says. “You need to have microbes to support plant growth, and that’s the primary source of any microbial contamination itself. It’s a natural balance, a symbiotic relationship.”
Growers with large operations have found that sanitary practices are not always sufficient — some strains encourage more microbial growth than others, while sometimes it is just up to chance. Sompalli, referring to his past experience at a federally-licensed cannabis producer, says it can be a challenging process.
“We have seen that no matter how clean your process is, it’s almost like guesswork.” One batch will pass; the other won’t. “It’s also strain-specific,” he says. “Some strains like a Kush—those dense strains—they’re hard to reduce moisture [which enables microbial growth].”
But not all producers see irradiation as inevitable. Craft growers say that consumers (especially those with a foot still in the legacy market) prefer non-irradiated cannabis. Jonathan Wilson of New Brunswick-based craft grower Crystal Cure says, “in my eyes, if a product has to be irradiated or remediated before it passes a microbial test, then I don’t consider that clean cannabis.” This echoes what any LP, even those who are irradiating, will tell you: irradiation does not exist to replace good microbial control practices, which are the most consequential factor on final microbial levels. “We prefer to be clean all the time and prevent things that would require remediation.” Being able to list one’s product as non-irradiated allows them to communicate this to consumers fairly quickly.
It also represents cost savings. “If we can avoid using it as a company, why wouldn’t we? Irradiation is a very costly process.”
Although federal organic regulations don’t apply to cannabis, some third-party organic certification agencies (such as the Fraser Valley Organic Producers’ Association, for example) require cannabis to be non-irradiated to receive the designation.
Critics of the process say that producers are over-irradiating. “Irradiation is abused in cannabis, in my opinion,” says Eidem. “For sure, in some contexts, these methods may be useful, specifically if a product is strictly medical and the intended use is for immunocompromised patients.” Eidem says that it’s common for producers to build irradiation into their production cycle because irradiation suppliers market it successfully. “Look at some of the irradiation company marketing,” she says. “It says stuff like ‘guaranteed passing,’ and ‘100% passing.’ They don’t talk about quality or integrating this step into their good manufacturing practices.
“People irradiate because it’s a guarantee that no matter what happens in their garden or during post-harvest, they can pass testing,” she argues. “Canada is miles ahead of the U.S. as far as good practices go, but they’re nowhere near where they should be.”
Is irradiation here to stay?
Given the industry’s comfort with the practice, irradiated cannabis is likely going to remain a valuable part of the production process. Done properly, it poses no risk to the end user on its own—though done improperly, Eidem says, it may have the ability to leech toxic chemicals from plastic packaging into the weed.
But others would still like the industry to shift away from irradiation, if only towards improved remediation techniques. Florina Truica, chief technical officer of the Cold Plasma Group in Kingston, Ont., believes her company’s cold plasma technique (which uses cold plasma gases to kill contaminants) offers an improvement. “Our plasma remediation cycles are optimized specifically for use with cannabis flower, balancing the kill efficiency with the need to protect the flower quality. For example, their appearance, the moisture, smell, as well as the precious phytochemicals contained in the cannabis flower,” she explains. “In addition, the treatment penetrates in all the pores of the flower from all directions, ensuring a complete and uniform treatment.” She also says that their cold plasma treatment machines are “several orders of magnitude cheaper, can be operated by the processors’ regular employees, and require only a small footprint of space for installation.”
Supporters of irradiation practices see the issue as a minor one, ultimately, that consumers will eventually forget about. “I think over time, all this will go to the back burner, and consumers will care about more specific things,” says Sompalli. “You consume spices every day—nobody is looking at the labels to see if it is irradiated or not. You are using, on a day-to-day basis, a product that is irradiated; cannabis is no different.”